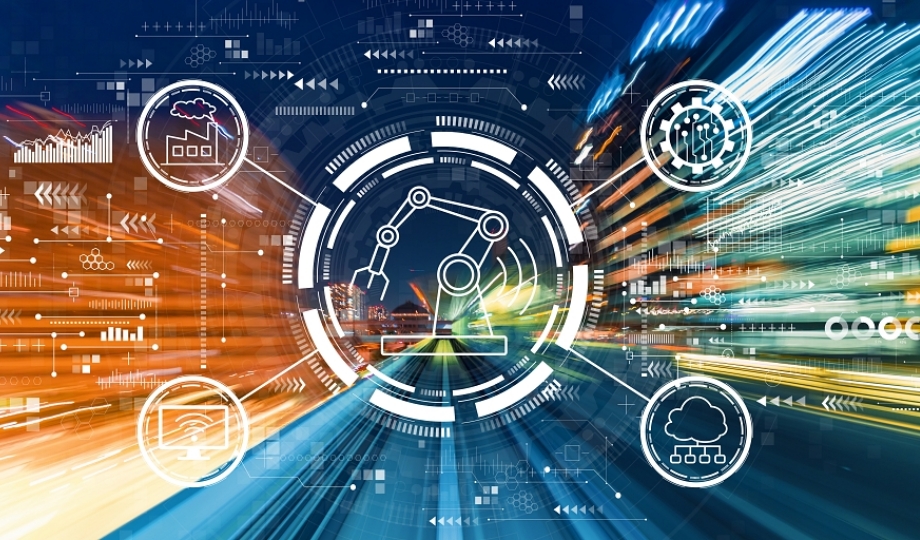
The future of industrial instrumentation involves integrating AI, IoT, smart sensors, and ML into technical training. Technicians use them to enable predictive maintenance, real-time optimization, and data-driven decision-making, ultimately leading to smarter, more efficient, and safer industrial operations.
Improved industrial instrumentation will lead to more efficient, connected, and optimized processes. Graduates well-versed in this discipline are in high demand in many businesses and industries.
AI And IoT in Industrial Instrumentation: Smart Sensors
The rise of smart sensors, IoT, and wireless instrumentation is making fast-paced strides in improving instrumentation in practice and technical training in the following ways:
- Smart Sensors: These sensors are at the forefront of modern process instrumentation. They provide real-time data, self-calibration, and enhanced accuracy, leading to more efficient operations. Smart sensors produce precision and accuracy for monitoring parameters in industrial operations. They are multi-functional by detecting several factors at the same time to provide a more complete picture of the working environment.
- IoT Integration: The Internet of Things (IoT) enables real-time data collection and connectivity in instrumentation, leading to smarter infrastructure and more responsive, adaptable systems.
- Wireless Instrumentation: Wireless instrumentation will play a significant role in the market in the next few years, allowing for easier deployment and maintenance.
AI And IoT in Industrial Instrumentation: Data Analytics And AI/ML
Real-time data analytics, artificial intelligence (AI), and machine learning (ML) are other tools playing significant roles in industrial instrumentation. The influx of data from smart sensors necessitates robust data analytics tools to process the vast amount of data in real time. They allow for quicker process optimization and more effective results.
AI and ML enable predictive maintenance, process optimization, and advanced decision-making capabilities. AI can detect anomalies in sensor readings and predict failures before they occur. AI and ML can continuously monitor equipment and identify early symptoms of wear and tear, enabling better predictive maintenance. They also reduce downtime by predicting scheduled repairs to eliminate stopping production lines and increase the life of machinery.
“Improved industrial instrumentation will lead to more efficient, connected, and optimized processes.” |
Automation And Autonomous Systems
Automation is a cornerstone of Industry 4.0, and instrumentation systems are no exception. It allows for the creation of intelligent, autonomous systems in widespread use today. Digital twins of instrumentation systems enable real-time simulation and analysis, resulting in greater accuracy and cost savings.
As instrumentation and control systems become more interconnected, addressing the associated cybersecurity challenges is crucial. Industry 4.0 brings a renewed focus on sustainability, including energy-efficient and environmentally friendly automation solutions. These tools can integrate effortlessly with automation systems to create autonomous control without human interaction.
Autonomous systems extend automation by allowing systems to make decisions and perform tasks with minimal human oversight, moving toward self-healing and predictive maintenance. They are built upon advancements in AI, robotics, IoT, and ML. Examples include autonomous mobile robots in warehouses, driverless vehicles in manufacturing, and AI-powered systems for process optimization…
Benefits Of Industrial Automation And Instrumentation
Technical students and company owners study the benefits of industrial automation and instrumentation. They seek to understand how these concepts create efficiency, safety, and higher business profits. The key benefits can include:
- Data-Driven Decision Making: Instrumentation provides real-time data that can be used to analyze performance, identify problems, and make informed decisions.
- Enhanced Product Quality: These systems can maintain consistent quality and reduce production errors
- Improved Safety: Automated systems can handle hazardous tasks, reducing the risk of accidents and protecting human workers.
- Increased Efficiency: Automation processes can lead to faster production, reduced waste, and optimized resource utilization.
- Increased Flexibility: Automation can be easily adapted to changing production requirements, including parts, products, and assembly.
- Reduced Costs: This technology can lead to lower labor costs, reduced downtime, and optimized energy consumption.
Industries That Use AI and IoT In Industrial Instrumentation
Many industries use AI and IoT in their instrumentation and production. Manufacturing uses automated product and assembly lines, robotics, and process control. Energy companies generate power, oil, and gas through production and distribution with AI and IoT. Chemical processing companies maintain optimal conditions for chemical reactions and ensure product quality.
Food and beverage businesses incorporate processing, automated packaging, and product quality control. Pharmaceuticals benefit by automating manufacturing, dispensing, and controlling product quality. Aerospace companies automate the assembly and testing of aircraft components. Water and wastewater treatment facilities monitor and control water quality and treatment processes.
AI and IoT will continue to play vital roles in industrial instrumentation and technical training. Contact ITI Technical College to learn more about our Instrument & Control Systems Technology (AOS) Associate In Occupational Studies Degree.
For more information about graduation rates, the median debt of students who completed the program, and other important information, please visit our website: https://iticollege.edu/disclosures/