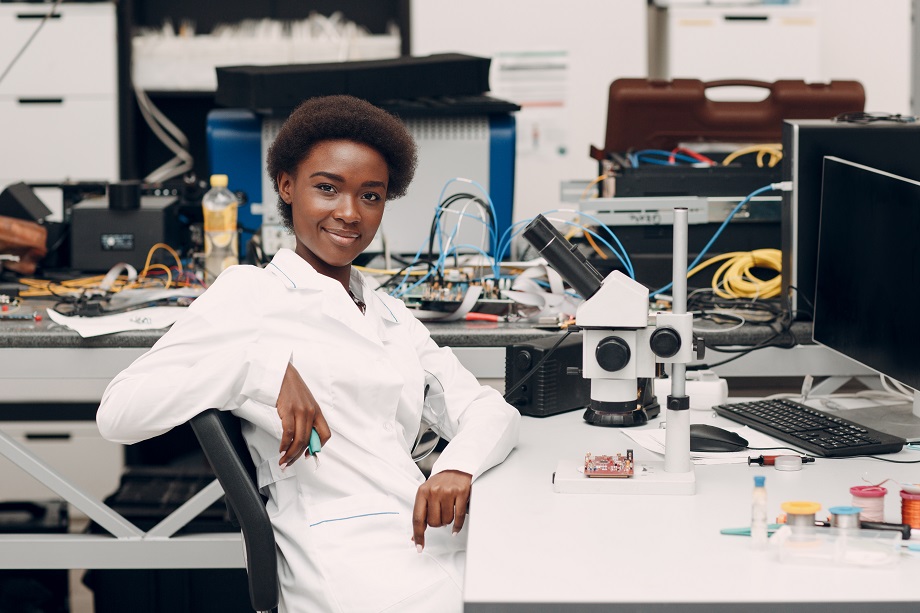
Manufacturers have been searching for ways to improve the production landscape for many years. They have trained workers more effectively, used robots, applied automation, and now use cobots. Cobots are collaborative robots that work with employees to achieve better results than either could achieve alone. Contact ITI Technical College today to learn more about cobots in manufacturing and their impact.
A Brief History Of Collaborative Robots And Cobots
The first cobot was invented in 1996 by J. Edward Colgate and Michael Peshkin who were professors at Northwestern University at the time. The term ‘cobot’ was coined by Brent Gillespie, a researcher at the same university. Cobot was originally explained as ‘a device and method for direct physical interaction between a person and a computer-controlled manipulator.’
Manufacturers saw the potential in robots and also began using cobots to improve production and efficiency. Kuka Robotics launched its first cobot in 2004 called the LBR3. Universal Robots released its first cobot in 2008 called the UR5. The UR10 was placed on the market in 2012 followed by the UR3 in 2015. Since then many models have been patented and put into production at many factories worldwide.
Robots Versus Cobots In Manufacturing
Traditional industrial robots are called non-collaborative robots because they work alone. They are used in large-scale operations with high volumes and repetitive tasks, such as welding and painting car bodies. Robots are typically stationary machines that can work at high speeds. Safety measures are used to ensure worker safety, such as safety cages. Robots are typically more costly than cobots and require extensive programming.
Cobots are called collaborative robots because they work alongside people in shared workspaces. Cobots are ideal for manufacturing products in lower volumes than robots. They prioritize human safety and are more adaptable for different tasks. Cobots typically are more cost-effective because they need simple programming and are more user-friendly.
“Manufacturers saw the potential in robots and also began using cobots to improve production and efficiency.” |
Why Companies Use Cobots In Manufacturing
Cobots are coming into their own globally because they offer many benefits to manufacturers and processing plants. They are changing the production landscape in many ways.
- Cobots offer a cost-effective way to automate repetitive tasks
- They improve production efficiency
- Cobots enhance work safety by doing hazardous jobs
- They provide flexibility to adapt to changing needs
- Cobots allow humans to focus on more complex tasks
- They free up workers to work with critical thinking and decision-making
Cobots require minimal setup and are generally easy to integrate into existing processes. They are ideal equipment for businesses on a budget because they are flexible, programmable, and have a positive team impact. Cobots are easily reprogrammed by moving the arm along the desired track. A Cobot will remember the new movement and repeat it on its own. Like robots, cobots can perform dangerous and repetitive tasks that boost productivity.
When To Use Cobots In Manufacturing
Cobots have their place in today’s manufacturing and processing facilities. Selecting the right automation machinery is critical and can hugely impact a company’s productivity and efficiency. Consultants have developed a general guideline for deciding when cobots should be used instead of robots.
- Budget limits favor cobots because they have lower upfront costs and are more employee-user-friendly
- Business needs, such as when a company wants to automate dangerous tasks instead of ramping up production favor cobots
- Environment and worker safety are superior to many robots because no cages or barriers are required that need extra space
- The nature of tasks favors cobots when more intricate tasks that benefit from human interactions such as assembly and quality control are required
- Small production businesses can use them to advantage because they are simple to program, do not need experts to maintain them, and work great for smaller production
- Volume requirements that are designed for smaller operations, flexibility, and adaptability better match up with cobots
Cobot And Robot Training Is Available Locally
If working with cobots, robots, and automation is your career goal, consider earning an Associate of Occupational Studies (AOS) Degree in Automation & Electronic Systems Technology at ITI Technical College. Our curriculum is current and our training is hands-on to maximize the development of your knowledge and skill sets.
Graduates are prepared to work in entry-level positions in various industries. Automation is revolutionizing the manufacturing industry and demand for trained workers is high. Don’t hesitate to contact us today for more information about this degree and our college. We look forward to serving you!
For more information about graduation rates, the median debt of students who completed the program, and other important information, please visit our website:https://iticollege.edu/disclosures/