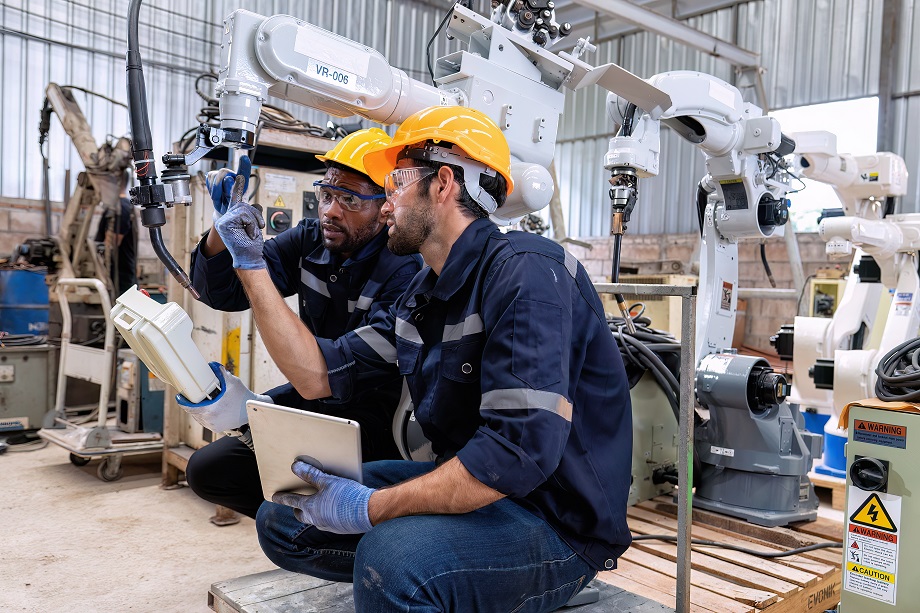
As manufacturing and processing facilities become more automated, worker well-being and safety become more critical factors, and industrial automation safety is a priority. Employees are exposed to more moving parts, robotics, programmed machinery, and artificial intelligence (AI) that carry with them some risk of injury.
General labor shortages have necessitated the development of automated systems to keep up with consumer demand. They must be implemented with worker safety in mind and not just higher productivity and quality. With careful planning and design, they can mesh together to achieve all anticipated goals.
Industrial automation safety starts with conducting a risk assessment, followed by worker training, implementation, and maintenance of the equipment. As global competitiveness increases, so will the need for advanced automation,
Risk Assessment In Industrial Automation Safety
The Oxford Dictionary defines risk as “exposing someone or something valued to danger, harm, or loss.” Manufacturing and processing plant owners and managers realize there are new risks involved when using new production equipment. Here are some recommendations to consider:
- Record the current unique workplace hazards
- Contemplate any new hazards automation may introduce
- Ask employees what factors they want to add
- Assign a scoring system to each factor on their likelihood and severity
- Determine where robotics and AI may improve workplace safety
- Determine where robotics and AI may threaten workplace safety
Managers must comply with all OSHA guidelines and state safety regulations. OSHA reports that failure to identify risks and hazards is one of the root causes of workplace injuries and deaths. Even one worker injury is too many!
Safety Protocols: Automate Slowly And Carefully
Experience has shown when managers introduce too many changes too quickly, it bothers people. This not only affects their general morale, it can create dangerous situations.
Industrial studies reveal that automation can reduce manufacturing injuries by up to 72% when implemented and followed correctly. These general guidelines for safety protocol should be followed from the first day:
- Divide the new systems into phases and implement one at a time
- Ensure connectivity between devices, machines, and systems in the network
- Train employees to be experts with the new automation tasks
- Allow robotics to perform the most dangerous processes that can harm humans
There are many industrial protocols and software programs available. Managers must purchase and implement those that are most effective for their specific needs.
“As manufacturing and processing facilities become more automated, worker well-being and safety become more critical factors.” |
Role Of Automation Engineers In Industrial Automation Safety
Industrial and electronic engineers are thinkers and designers who keep safety in mind in any new system. Automation technicians work with them to accomplish these goals:
- Ensure that industrial processes are automated correctly
- See that IoT-enabled devices and systems are secure and reliable
- Ensure that IoT systems meet a business’s unique needs
- Eliminate defects, errors, and problems with products and software
- Ensure that business and customer service processes function correctly
Engineers and technicians also look for more opportunities to implement automation in processes. They also run tests, improve quality, and gather information from customers and end-users. Their ultimate goals are to improve efficiency, worker safety, performance, and system maintenance.
Role Of Automation Technicians
Automation technicians should receive formal training at a postsecondary institution before starting a job or career. Once hired, they must familiarize themselves with their duties and roles to maximize daily safety. These general guidelines should be followed:
- Maintain the equipment to ensure safe and efficient operation
- Report any malfunctions immediately to supervisors
- Do not expose yourself to any unnecessary danger
- Do not take chances with the unknown
- Develop basic first-aid skills where necessary
- See that co-workers observe safety protocols
Automation technicians are in daily contact with devices, equipment, machinery, and systems used in manufacturing and processing systems. They regularly collaborate with cross-functional teams that include engineers, programmers, operators, and maintenance personnel to create and prioritize safer work practices.
Comprehensive Training Is Critical
Employers prefer new hires who are trained in essential knowledge and skills in automation systems. Having a college degree on your resume and intelligently discussing automation in job interviews helps set the stage for being hired.
The best training advice is acquiring an Associate of Occupational Studies (AOS) Degree in a comprehensive Automation and Electronic Systems Technology training program. This degree provides the foundation of skills and knowledge to obtain an entry-level job in a variety of industries. Now is the time to explore this fascinating and rewarding career with a college admissions representative. Contact us today for more information.
For more information about graduation rates, the median debt of students who completed the program, and other important information, please visit our website: https://www.iticollege.edu/disclosures