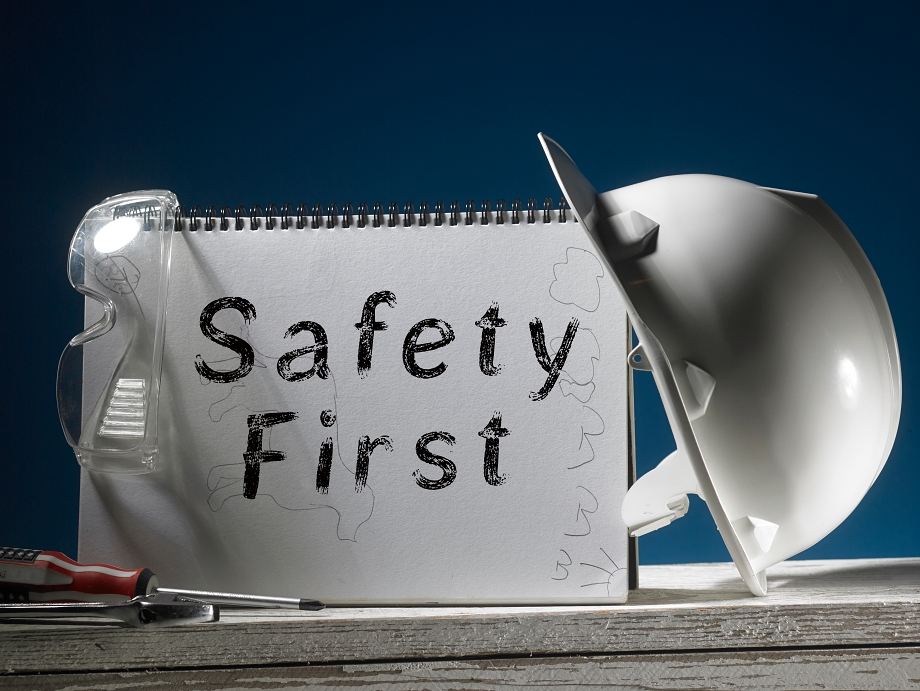
Safety in construction management means protecting workers and others from injury, disease, death, and other health risks. It also involves preventing damage to equipment, buildings, tools, and the surrounding area. Although managers supervise workplace safety, technicians are the ones who are typically hurt due to more exposure on the job site. Contact ITI Technical College today for more information.
Technicians often take some safety protocols for granted and can become careless or complacent about them. At times, they think that accidents and injuries won’t happen to them because they always happen to someone else. They also feel they have the experience, skills, and knowledge to avoid these problems, but in reality, sometimes they are not prepared for what could happen to them and others.
Why Do We Need Safety Protocols in Construction Management?
Good construction site safety protocols decrease the risk of injuries and accidents to workers and the public. OSHA estimates that nearly 25% of work-related fatalities occur in the construction industry. A higher percentage of injuries that do not lead to death are present in this industry. The most common safety and health-related issues include (in no certain order):
- Caught in or between materials, equipment, or structures
- Chemical hazards cause respiratory, eye, skin, cancer, and chronic illnesses
- Electrical shocks or electrocutions cause burns and deaths
- Falls, slips, and trips – falls are the leading cause of deaths and injuries
- Hand-arm vibration syndrome caused by long-term use of hand-held tools
- High temperatures can cause serious burns or loss of some physical function
- Materials that are overloaded, loaded off-center, or not handled well on equipment
- Struck by heavy construction equipment
Most safety and health issues affect construction technicians who are active on the job rather than managers or the public. They must be aware of and follow all safety protocols to ensure their or other people’s safety.
Benefits Of Safety Management And Leadership On The Job Site
Safety protocols must evolve to match new construction processes and technologies, and they should meet OSHA standards. When construction managers put safety first, they protect their workers, themselves, and the public in ways that benefit all of them, including:
- Reduced liabilities
- Reduced costs
- Enhanced productivity
- Improved quality
- A more committed and resilient workforce
- Fewer and less severe incidents
Construction owners and managers must develop a strong safety and health program that contains multiple interrelated elements. The best companies with the least injuries are doing it and so should all other companies.
“Although managers supervise workplace safety, the technicians are the ones that are typically hurt due to more exposure on the job site.” |
Develop A Plan For Safety Protocols In Construction Management
A successful safety and health job site plan begins with developing a culture of safety from the bottom up based on an effective plan. Once developed, construction managers must train technicians and other managers to follow the established protocols. Here are the essential components of a viable and effective working plan:
- Hazard Identification and Risk Assessment – Managers must regularly identify current and potential hazards on site and evaluate their risks.
- Safety Policies and Procedures – These guidelines must be developed and enforced to govern workers’ actions and ensure consistent safety measures.
- Emergency Preparedness – Managers and technicians must be prepared to respond quickly and effectively to unexpected incidents. They range from accidents, death, sickness, and natural disasters.
- Training and Competence – All employees must be properly trained in safety and health issues and deemed competent to carry out their daily tasks safely.
- Incident Investigation – All incidents must be thoroughly analyzed to determine the root cause and measures that were implemented to prevent recurring incidents.
- Performance Measurement – Leaders should monitor and measure the safety performance of workers to identify areas for improvement.
From technicians’ perspectives, they may see some parts of the plan as unnecessary and show resistance to them. They may think they know enough through experience and have never violated any policies. Thinking this way is always a mistake because conditions change and hazards evolve.
Technicians Should Use Safety Management Software
Technicians and managers use safety management software as indispensable tools for safety and productivity. They find these platforms can streamline safety awareness and processes by:
- Automating compliance tracking Insert Adobe Image
- Understanding risk assessment better
- Improved incident reporting tasks
- Having a centralized database
- Monitoring safety metrics
- Tracking improvements
Safety management software has data analysis capabilities that provide quicker responses to potential risks that enhance the company’s overall safety strategy.
What Many Construction Workers Think
In the end, many construction workers think their employers should do more to enhance their safety. Some think they are pressured to stress productivity over worker safety and have a fear of reporting incidents that point out failures. Others feel they are put into too many unsafe conditions and fear falling. Their best options include taking all safety training and discussing issues with managers before being put into questionable circumstances.
Learn more about a career in construction management and workplace safety at ITI Technical College in Baton Rouge.
For more information about graduation rates, the median debt of students who completed the program, and other important information, please visit our website: https://iticollege.edu/disclosures/