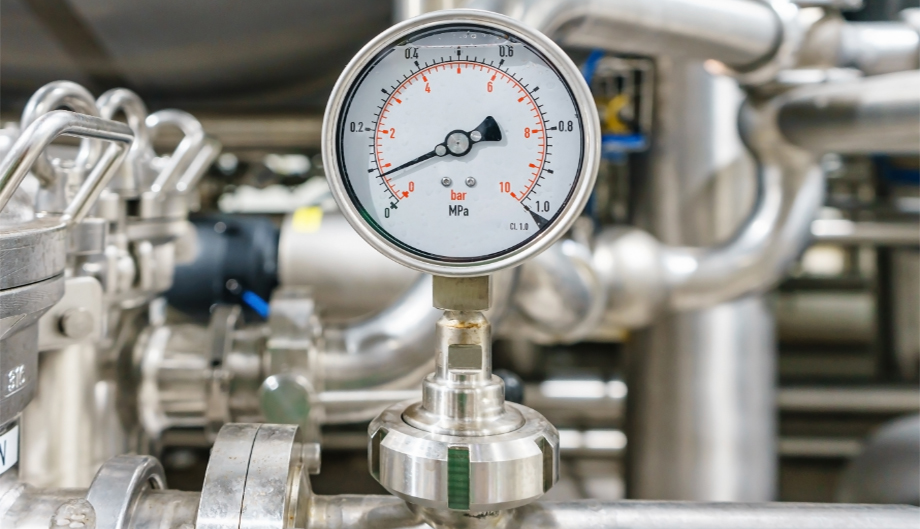
Although there may be some technicians still on the job without a college degree, this is considered ‘old school.’ They were probably hired many years ago when higher education was not required and experience on the job substituted for it. Today, to obtain the benefits of Instrumentation and Control Systems employment you need an associate degree.
The benefits of earning and applying for a college degree on the job include:
- Acquiring the skills needed for career success
- Gaining all-around knowledge for job success
- The ability to comprehend large volumes of written content, such as training manuals, detailed written project instructions, and repair manuals
- How to work closely with engineers and managers
- The best way to land an initial entry-level job
Each of these is explained further in the following comments for your information.
Benefits of Instrumentation and Control Systems Includes Acquiring Skills for Career Success
Skills are related to knowledge of a job but apply to what you can do with that knowledge. Honed skills are one of the significant benefits an instrumentation and control systems technician acquires during college training. These essential skills include:
- Installing, maintaining, and troubleshooting equipment and instruments
- Metering, sensing, and controlling physical quantities, such as flow rate, power, pressure, temperature, volume, and voltage for measuring and controlling processes
- Using actuators, controllers, data acquisition systems, sensors, and transmitters to measure equipment and instrument performance
- Coordinating instrumentation with motors, turbines, and other machinery, and computer technology
- Adjusting, repairing, and replacing devices and equipment
- Ability to study schematics and blueprints of system components to assemble parts and analyze their features for measuring and controlling
All these skills provide college graduates with the personal tools needed for success as instrumentation and control systems technicians.
Benefits of Instrumentation and Control Systems Includes Gaining Knowledge for Job Success
Gaining an adequate working knowledge of instrumentation and control systems is broken down into two parts. Instrument systems for measuring applications and processes are called instrumentation. Instrument systems for controlling equipment are known as process control.
This type of work is a subfield of electrical engineering where technicians work closely with engineers, supervisors, and plant operators. Technicians learn to:
- Record and report data from their findings
- Work in a manufacturing or processing plant facility
- Understand an overall working knowledge of this industry
- Work safely and efficiently within the company’s operating system
- Collect environment data and monitor the pollution output (if any) of the plant
Each company and industry may require additional knowledge that can be acquired in college or on-the-job training.
“Today, to obtain the benefits of Instrumentation and Control Systems employment you need an associate degree.” |
Learning How to Comprehend Training Manuals and Written Instructions
One of the benefits of graduating from a technical college is learning to read and comprehend large volumes of information such as training manuals, written project instructions, and repair manuals. All the classroom and lab studies prepare students to understand what they read and how to communicate orally and in printed form.
This comprehension ability is necessary to quickly understand dealing with large quantities of details, the jobs at hand, and take effective action. Students also learn they don’t need to be afraid of asking questions when they need help.
Learning How to Work Closely with Engineers and Managers
Another benefit of an instrumentation and control systems degree is learning to work effectively with engineers, supervisors, and plant operators. The time spent working with instructors, mentors, other students, and career services counselors is great preparation for actual work experience.
The Career Services Office Assists Students with Landing an Entry-level Job
A college career services office employs counselors to assist students with a wide range of job-seeking knowledge and skills. They help graduates find entry-level jobs in these positions:
- Instrument fitter, instrumentation repair/maintenance technician
- Analyzer technician, assistant instrumentation designer
- Instrument sales representative for manufacturers and distributors
- Technicians in energy companies such as oil, gas, and renewables
- Technicians in aerospace, chemicals, food processing, pharmaceuticals, transport equipment, and water/wastewater plants
If you want the benefits of an instrumentation and control systems degree, be sure you work closely with the career services office.
For more information about graduation rates, the median debt of students who completed the program, and other important information, please visit our website: https://www.iticollege.edu/disclosures